Brands seeking bio-based alternatives for commonly used stretch materials — elastane being one — face long R&D lead times, big investment outlays, and complexity finding the right suppliers.
That’s why a group of leading fashion brands, including PVH Corp, Ralph Lauren, and Reformation, undertook a collaborative project facilitated by Materiom and the Ellen MacArthur Foundation to assess the innovation landscape for bio-based elastane alternatives. A subsequent project, led by Materiom, will focus on practical experimentation with a group of high-potential partners.
The landscape overview spotlights 46 high-potential suppliers of bio-based elastane alternatives globally. Elastane, also known as spandex, is a synthetic stretch fiber used in many clothes for its elasticity and comfort, but its use raises significant environmental concerns.
The challenge with synthetic stretch fibers
When elastane-containing garments are washed, their synthetic fibers shed and find their way into rivers, lakes, and oceans in the form of microplastics. Although elastane makes up only a small percentage of each garment, fabric blends containing the material are challenging — if not impossible — to recycle.
While commonly used yarns like cotton are readily recyclable in their pure form, adding even the smallest amount of elastane creates complications for conventional separation and recycling techniques. As a result, most elastane-containing garments are disposed of as mixed waste, reducing opportunities to convert waste into value.
Bio-based innovators rising to the challenge
As brands demand bio-based alternatives that meet their environmental and social responsibility targets, material developers are responding with a range of novel solutions. Examples include:
- Canadian startup TIRA uses rice husks, food waste, and non-toxic additives to produce a 100% bio-based replacement to elastane through extrusion rather than wet spinning
- US-based Yulex produces a commercial filament stretch fibre made from natural latex / rubber, sourced from smallholder farms centering social and environmental equity
- UK-based Nanoloom uses nanotechnology and graphene, a carbon allotrope that can be extracted from graphite or waste biomass, to create a range of non-toxic, biodegradable, and recyclable fibers
- Spideytek uses the alfalfa plant to make recombinant spider silk proteins that can be turned into a bio-based elastane alternative through wet spinning
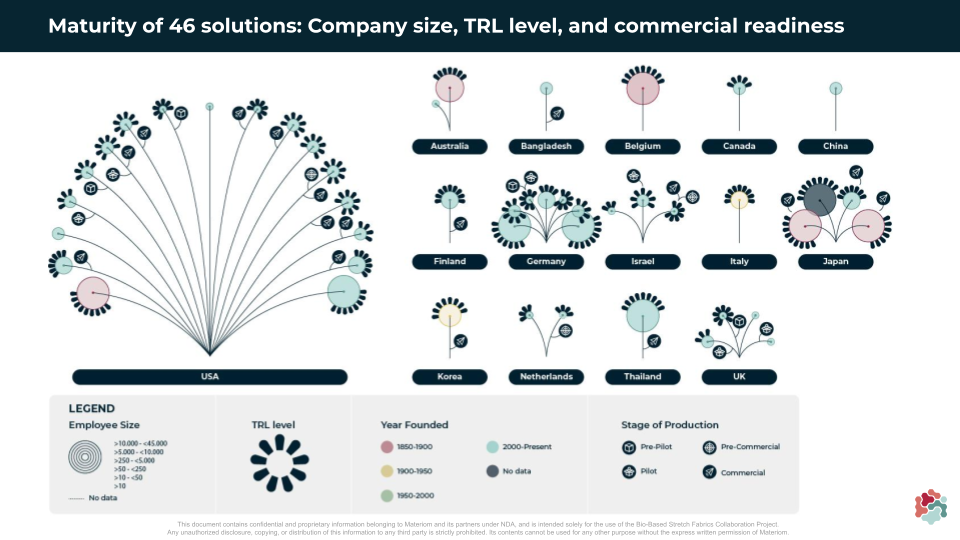
The 46 bio-based stretch fiber solutions profiled in the landscape overview originate in 15 countries, with the majority from the USA. The maturity and commercial readiness of the solutions vary — many are still in pilot or pre-pilot stages of production with low to medium technology readiness levels (TRLs). 13% have bio-based content certifications, 21% are reported fully or partially biodegradable, and just 4% are reported to be recyclable.
Collaboration is key
Cohort discussions revealed a strong need to connect with industry partners to scale adoption.
“Long, iterative R&D cycles and finding suitable innovation partners — particularly further up the supply chain — are common challenges for brands,” said Steve Diacono, Strategic Design Manager at the Ellen MacArthur Foundation.
“Creating a pre-competitive environment that encourages shared learning and investment is critical to unlock participation and speed up innovation.”
Cohort learnings for successful collaborations with supply chain partners included sharing industry specifications and clear non-negotiables up front — such as bio-based content and separability — and understanding requirements for performance, machining, and processing early on.
Assessing the environmental impacts of novel bio-based materials was another key focus. Experts were consulted to share knowledge on the topics of microfiber pollution and biodegradability, feedstock sourcing, material processing, and circularity considerations.
Lauren Bright, Textiles Specialist at Materiom, said: “This landscape overview and assessment is a first step in building collaborative industry momentum for bio-based stretch fabrics. The innovators profiled represent a wealth of potential and it is inspiring to engage with brands whose intentions are not only to support their own company goals, but to progress the industry as a whole.”
Brands and other organisations — supply chain partners, technical specialists, philanthropists, and non-profits — interested in collaborating in a subsequent innovation project are invited to get in touch via hello@materiom.org